They might look like relatively straightforward sporting equipment, yet the reality of how a hockey stick is made requires a complex answer. It actually involves a very detailed process, using space-age materials and manufacturing techniques that require skill, experience, precision and an eye for detail.
The origins of ice hockey are the subject of much debate amongst sports historians, but it’s generally agreed that the hockey stick developed from a number of ‘stick and ball’ games from the UK. These include ‘shinty’ from Scotland, ‘hurling’ from Ireland and ‘bandy’ from England, a very early form of ice hockey played with a ball instead of a puck.
The first organised game of ice hockey took place at the Victoria Skating Rink in Montreal, Canada, in 1875. It was played between two teams of nine (today it is six-a-side) and early sticks were hand-whittled from maple or willow.
Ash became the wood of choice in the 1920s, and there was then very little development in stick technology until the late 1990s – with the advent of strong, flexible and lightweight materials such as carbon fibre. So how are hockey sticks made?
Types of Hockey Sticks - Composites vs Wood
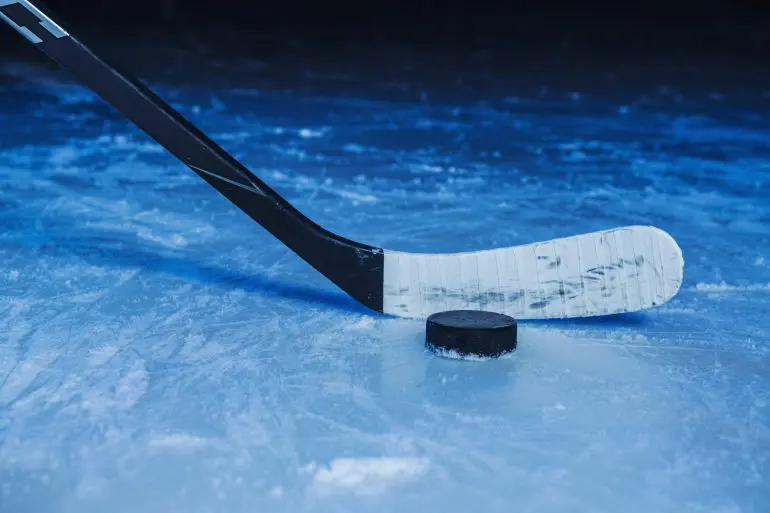
Hockey stick and puck (Photo: Erik Isakson via Getty Images)
There are two main types of stick – wooden hockey sticks and composite hockey sticks – and which one you opt for is all down to personal preference.
Wooden hockey sticks have been used since the birth of the sport. They are cheaper than their composite cousins, and players who choose wood often say that they feel much more of a connection to the stick when receiving passes or shooting for goal. A downside of the wooden variety is in how hockey sticks are made, especially when it comes to the top amateur and professional ranks. Every piece of wood is different so it’s very hard to get consistency. It would be like a tennis player playing with rackets that have different string tensions.
Composite hockey sticks on the other hand are made of a variety of materials, including fibreglass, Kevlar, and carbon fibre. The shaft of the stick is usually made of carbon fibre, while the blade is made of fibreglass or another material. Carbon fibre is used as it can withstand a significant amount of force without breaking, while it’s also very lightweight. The materials are layered together and then moulded into the desired shape. While composite hockey sticks are lightweight, strong and durable, they do tend to be more expensive than other types of hockey sticks.
At the higher echelons of the sport, composite hockey sticks are used by virtually all professional players. Much of the reason for choosing this type of stick comes down to the answer to the question ‘how are composite hockey sticks made?’ Although they’re more expensive than wood, composite sticks are lighter, more durable and can even be custom made to very exact specifications. In addition, many players say they are more powerful than wooden sticks, they don’t vibrate as much and are much more consistent.
As composite sticks are now the professional standard, when it comes to how hockey sticks are manufactured today, we’ll focus here on how composite hockey sticks are made.
The First Period - How Do You Make a Hockey Stick?
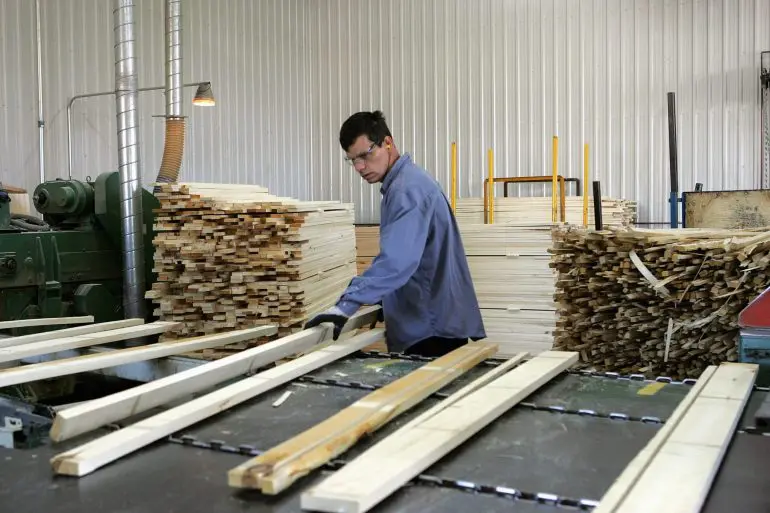
Preparing wood for the making of hockey sticks (Photo: Bruce Bennett via Getty Images)
First, the official NHL rules. A hockey stick must be no longer than 63 inches long with a blade length of no more than 12.5 inches and a blade width of between 3 – 4 inches. Players who are taller than 6’6” can have a stick up to 65 inches long, but need written permission from the league.
Now let’s find out how hockey sticks are made.
First, sheets of carbon fibre are laid across each other to make an incredibly strong yet light material. This is squeezed through a heated roller that melts the layers together into one sheet of composite fabric. The strips are then cut to size, and between 15 and 20 layers are wrapped around a hollow core.
The carbon fibre-wrapped shafts are now placed in compression tubes, and heated to around 150°C which fuses the layers together until they are virtually unbreakable. The core is removed, and when they’ve cooled sufficiently, a machine tests the flexibility to ensure they can cope with the pressure of a world class ice-hockey player shooting for goal. The greater the flexibility, the greater the torque, the harder the shot.
The Second Period - Blade Runner
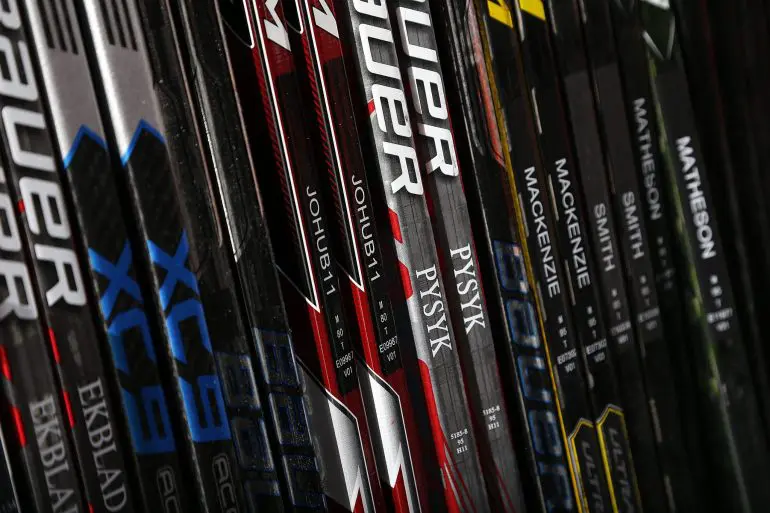
Various Hockey sticks (Photo: Eliot J. Schechter via Getty Images)
As the shafts undergo stress tests, the outer surface of the blades are precisely machine-cut from the same layered carbon fibre that is used to create the shafts.
The inner core of the blade is made from a rubber bladder, surrounded by two pieces of foam. The foam cushions the immense forces that players use to hit the pucks.
To protect the core, 35 layers of carbon fibre are wrapped around it. Similar to the shafts, the blades are heated and pressed inside moulds to bind the layers together with eight tons of downward force. It’s this constant wrapping, heating and binding that gives the stick its strength and explains how hockey sticks are made.
At the same time, the inner bladder inflates, compressing the carbon fibre from the inside.
When the blades are released from the moulds and have cooled down, the shafts are slotted into the blades using ultra-strong glue.
When the adhesive is set, the ice hockey sticks go through a rigorous quality control process.
For one manufacturer, random sticks are selected that have to hit 200 pucks at a speed of 75mph without shattering. If one does, the entire batch is discarded.
The Third Period - The End Game
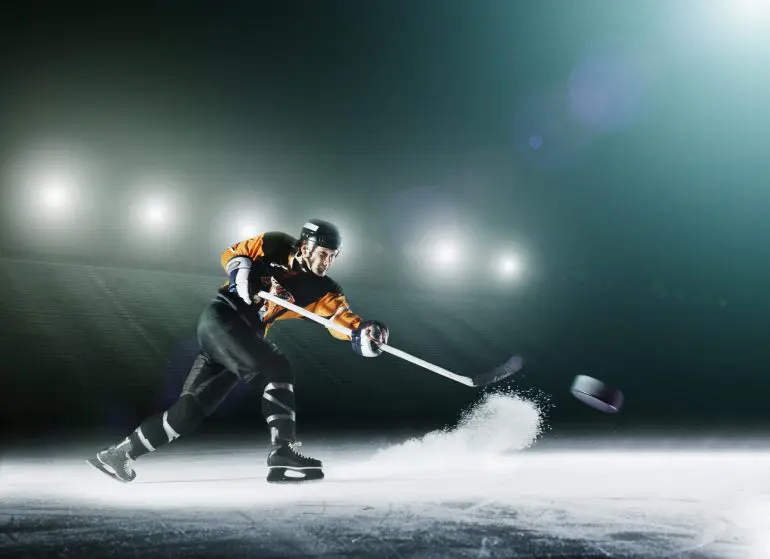
A hockey player in action (Photo: Dmytro Aksonov via Getty Images)
Providing they pass quality control, the sticks are now painted, the manufacturer’s logos are applied and each stick is coated in a protective layer of resin, which gives the players a firmer grip. Finally, a plastic plug is inserted into the open end at the top of the shaft.
Amazingly, the process of how hockey sticks are made takes just two hours from start to finish, a lot faster than some sports (such as the 23 days pool balls take to make!)
So this answers the question ‘how are composite hockey sticks made’. Next time you’re on the ice and one of your opponents politely asks, you’ll be able to tell them!