Chewing Gum was first sold in 1848 by an American businessman called John Curtis, who called it The State of Maine Pure Spruce Gum. It didn’t quite have the marketing ring of Hubba Bubba or Bubblicious.
To keep it sweet, chewers would keep a bowl of powdered sugar to hand and dip the gum into it from time to time. By the end of the nineteenth century, chewing gum was increasingly popular and the market was getting crowded, but Frank Fleer of Philadelphia wanted something different. He wanted to make gum that his customers could blow bubbles with.
This is the story of how bubble gum is manufactured.
Bubble Gum - A Short History
If you want to know how was bubblegum invented, ask an accountant. Seriously! In around 1906, the Frank H. Fleer Corporation tried to perfect a bubblegum recipe, but it was far too sticky and could only be removed from surfaces with turpentine.
Twenty years later, Fleer company accountant Walt Diemer, who used to experiment with how bubble gum is made in his spare time, eventually stumbled on a formula that worked. A soft, chewy gum that people could blow bubbles with. The only trouble was that it was grey and visually unappealing. The only food colouring they had in the factory was pink, and they sold it as Dubble Bubble. This is why even today, bubblegum is usually pink.
Today’s manufacturing processes are vastly different to Walt Diemer’s time, so how do you make bubble gum? Here’s the answer.
How Bubblegum is Made
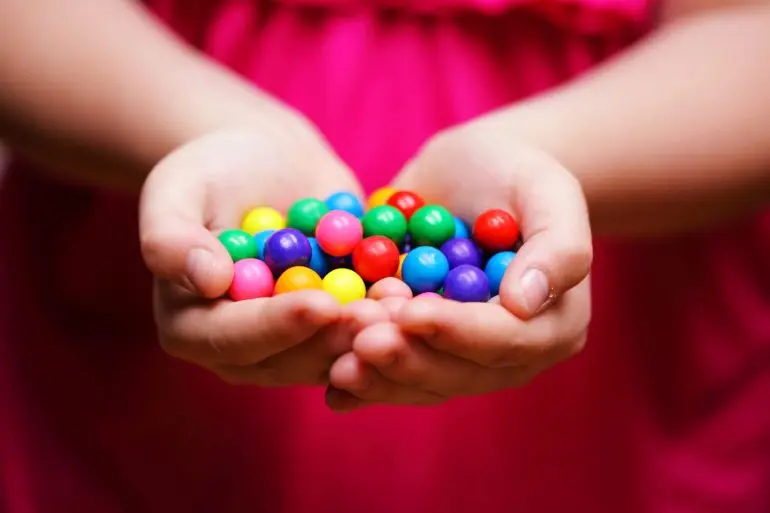
Child Holding Colourful Gum Balls (Photo: D. Sharon Pruitt Pink Sherbet Photography via Getty Images)
Until the 1940s, gum was made with chicle, the naturally-occurring gum from the sapodilla tree. However, this became scarcer and eventually prohibitively expensive, so manufacturers resorted to synthetic compounds. As always, the people who make products such as chocolate or popcorn won’t give out their exact recipes or manufacturing process, but generally speaking, this is how bubblegum is manufactured.
The gum base starts as small pellets of plastic and rubber, to which colour and flavouring is added. It is mixed together in a huge drum, then glucose syrup is added both for sweetness and to keep the gum soft and chewy. In addition to the base, preservatives and other sweeteners like dextrose or xylitol are included in the recipe.
The gum mixture is heated via the friction of the stirring, and is blended for around half an hour until it all melts into a huge pink blob. When the mix reaches the consistency of bread dough, it’s ready for the next stage and into the pre-extruder.
The pre-extruder is a machine which squeezes the huge mass of pink gum through a narrow opening – like squeezing toothpaste out the tube – ready for the extruders, which shape the final product. This is where the magic happens on the journey of how bubble gum is made. These huge machines squeeze the gum into the width of the finished piece of gum, although it’s hundreds of metres long! The extruders also heat the gum and if it were to be cut and packed at this stage it would stick to the inside of the wrapper.
The Cut ‘n’ Wrap
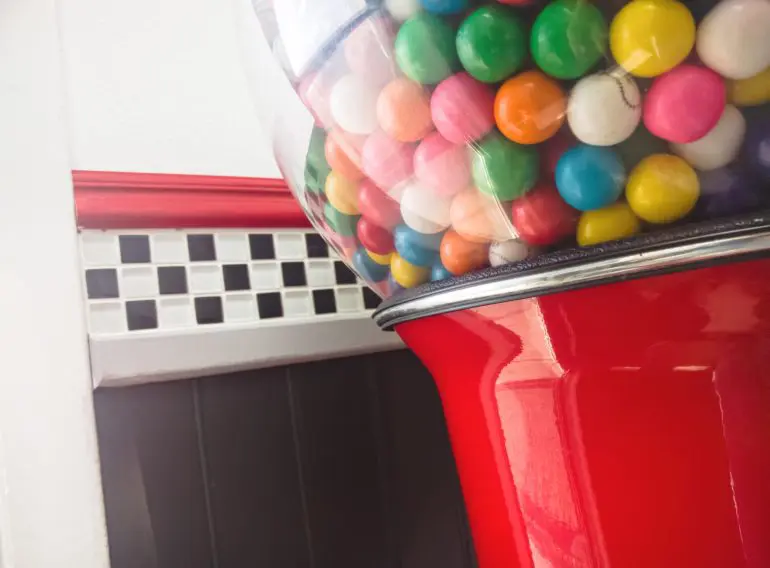
Closeup of a gumball machine (Photo: harpazo_hope via Getty Images)
At this point in the process, the hot gum becomes cold gum. It is cooled in a refrigerated chamber at a temperature of between 3-7°C. Once cooled, it’s now ready to be cut into pieces and wrapped, known in the trade as the cut ‘n’ wrap.
The machine slices off the correctly sized pieces and in the same action wraps it and twists the ends of the paper at a rate of around 900 per minute. In an eight-hour day, that’s a staggering 432,000 pieces of gum, surely enough to keep Violet Beauregarde busy!
Of course the specific processes of how bubblegum is manufactured differs from company to company. Some types of bubblegum are wrapped in aluminium-backed paper, others in tubes and others not at all, like gumballs for example, but this is generally the process for how bubble gum is made.