Making a cricket bat is an artform. They may look like simple pieces of wood, but in fact it takes skilled craftsmen many years to learn how cricket bats are manufactured.
If you start at the beginning, the very first cricket bats resembled hockey sticks – the world’s oldest bat dates from 1729 – and in the 1750s they looked more like small rowing boat oars. It wasn’t until the 1770s that cricket bats took on the familiar shape we know today.
Over the next 250 years, the general shape hasn’t changed too much. Back then they were whittled, shaped, shaved and sanded by hand, yet while the shape may still be the same, the manufacturing process has changed beyond all recognition.
Modern-day cricket bats go through a far more complex and specialist process to ensure they’re as high quality as possible, and the detail involved in how cricket bats are made is truly astonishing.
What Wood is Used to Make Cricket Bats?
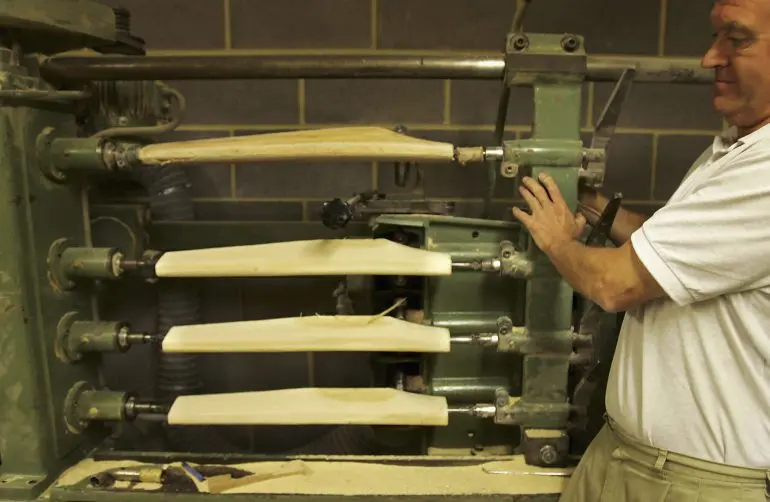
Blanks of willow are carved into cricket bats (Photo: Bruno Vincent via Getty Images)
Cricket bats are made from wood from the English willow tree (Salix alba var. caerulea). Willow is used because it is light, yet hard-wearing and durable. It also doesn’t dent, splinter or fracture when coming into contact with a high-velocity cricket ball, even those moving at up to 100 mph from the world’s fastest bowlers. The quality of the willow is also very important and the wood used is graded for its quality, much like diamonds.
Grade 1+ English Willow – the finest quality unbleached wood with approximately 8-12 clean, straight grains that are free of blemishes.
Grade 1 English Willow – similar to 1+ but with slightly fewer and wider straight grains.
Grade 2 English Willow – A slightly irregular grain with small blemishes such as heartwood or twig marks to the wood. Unbleached.
Grade 3 English Willow – Some will be bleached to mask an irregular grain and prominent blemishes to the wood including more heartwood.
Willow trees also grow in Kashmir in the Indian subcontinent, and bats are made from this variety of the tree. Some say it performs no differently to English willow bats, while others are of the opinion that it is harder and dryer and doesn’t play as well at the highest levels of the game – though players are unsure why and how, and this remains highly speculative.
Cricket bats are manufactured in exactly the same way both in the UK and elsewhere around the world.
From Tree to Test Match - How are Cricket Bats Produced?
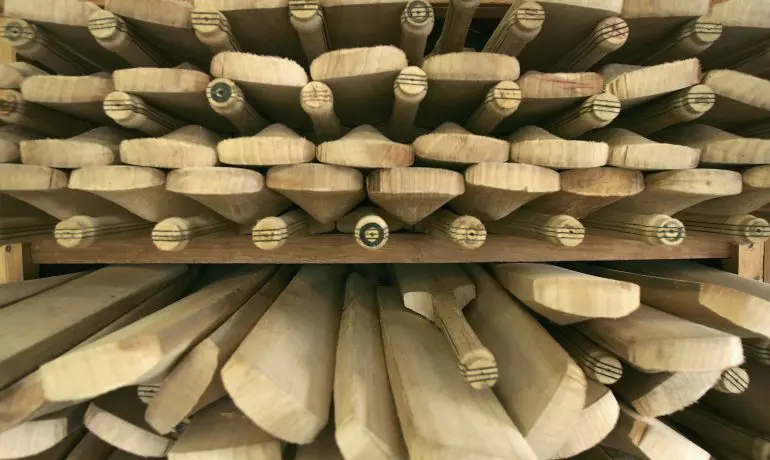
Cricket bats are seen waiting to be finished (Photo: Bruno Vincent via Getty Images)
In the Laws of Cricket, Law 5 states that a cricket bat may be no longer than 96.5cm long, 10.8cm wide, and have an overall depth of 6.7cm with an edge of no more than 4cm. So once the dimensions of any newly designed bat are confirmed as legal, how are these cricket bats produced? Well, the whole process is made up of a number of key stages:
Stage 1 -The Wood
The best cuts from the willow tree are taken by very skilled lumberjacks. They will look to use the sapwood, which grows under the bark. It is the newest wood and is more pliable.
After the wood is sawn from the tree, it is carved into chunks known as clefts. Before they are moulded into their final shape, the pieces of willow are air-dried for anything up to a year to remove moisture. This is a very important process and vital to a finely-balanced bat used by the world’s top professionals.
At this stage the wood is graded. The clefts are then cut to the approximate shape of the finished bat.
Stage 2 – The Pressing
If you’ve ever wondered how cricket bats are manufactured, it’s not as straightforward as you might think. The cut cleft is then put through a very heavy rolling machine to press the bat into shape, known as a ‘blade’. It also curves the blade of the bat and compresses the wood’s fibres to give the bat more structural integrity.
Stage 3 – The Handle
The handle of the cricket bat is made from a composition of cane and rubber strips to give it rigidity but also a measure of elasticity to protect the player’s wrists and forearms. The top of the blade is spliced into a deep ‘V’ shape and the handle is pushed into the gap. It is sealed using a strong, specialist bonding agent and then clamped together and left to dry.
The handle is bound using a linen thread and secured with glue. This is one of the most important elements of how cricket bats are made.
Stage 4 – The Details
By now, the bat is almost complete and the very best bats – which can cost over £400 – are hand-finished. The shoulders (where the handle meets the blade) are cut out and small, delicate shavings are made by eye by highly-skilled craftsmen.
Once the edges have been machine- and hand-sanded to make them smooth, the new bat is polished using a compound wax. Lastly, the manufacturer’s stickers are added and the rubber grip is applied to the handle.
There’s No Such Thing as a One Size Fits All Cricket Bat
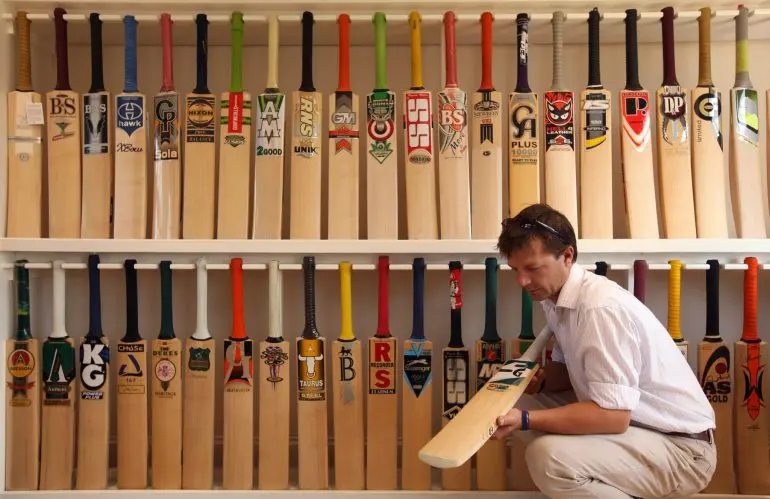
Inspecting a selection of cricket bats after the production process is complete. (Photo: by Oli Scarff via Getty Images)
Of course over the years there have been many attempts to change the design and materials of the classic bat. In 1979 Australian batsman Dennis Lillee walked to the crease with an aluminium bat and – for a short while in the Twenty20 series – some batsmen used the Mongoose. It had a very long handle and a smaller batting surface, supposedly providing the hitter with a bigger sweet spot to rack up bigger scores more quickly. Yet, despite these attempts at innovation, the classic willow and standard shape of cricket bats continues to go from strength to strength, and there’s no sign of a revolution any time soon.