They say money makes the world go round and it’s probably true. For thousands of years, almost every civilisation has used coins in one form or another.
Today, the Royal Mint in the small town of Llantrisant in North Wales makes an incredible 3.3 billion coins every year. If you think that’s a lot, the US Mint can produce over 25 billion coins a year! Here, we’ll tell you all about the coin manufacturing process and how coins get from design to dough!
How were Ancient Coins Made?
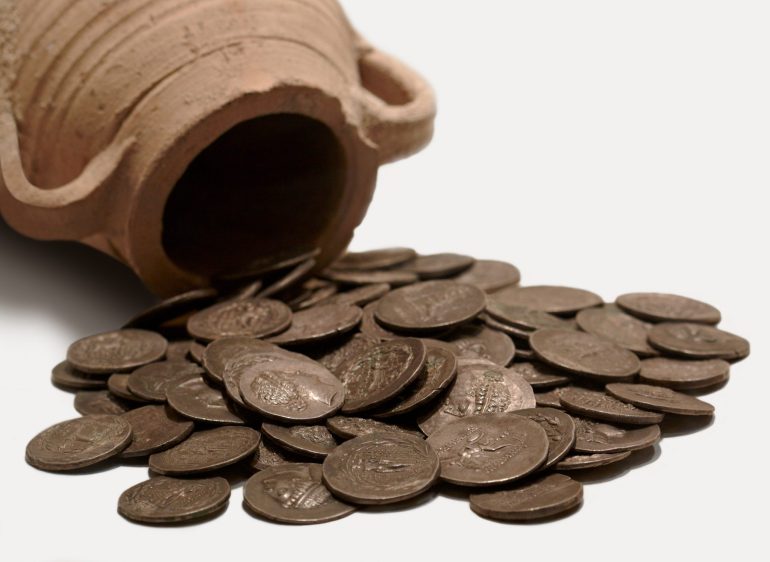
A pot of ancient coins (Photo: hdagli via Getty Images)
Among the earliest coins ever produced were those created in the kingdom of Lydia, in modern-day Turkey, around 700 BC. Many of these ancient coins were excavated from the site of the Temple of Artemis at Ephesus, one of the Seven Wonders of the Ancient World. They were made from a variety of metals including gold, silver and electrum, an alloy of both.
The production process of these historic coins was relatively straightforward. The irregular-sized pieces of metal would be heated over a flame and stamped with an imprint of an animal such as a lion or bull and then left to cool. These were known as punch-marked coins.
From around 480 BC, the ancient Greeks made beautiful coins of silver and gold with images of deities and the name of the issuing city. A century and a half later, the habit of dynastic portraiture, that is, an image of the reigning king or queen became popular.
The coin manufacturing process changed very little for hundreds of years until the Romans got involved. In fact the word ‘mint’ comes from a silver coin made at the Roman temple of Juno Moneta. The name of the British currency comes from the Latin ‘libra pondo’ which translates as ‘a pound by weight.’
How were Roman Coins Made?
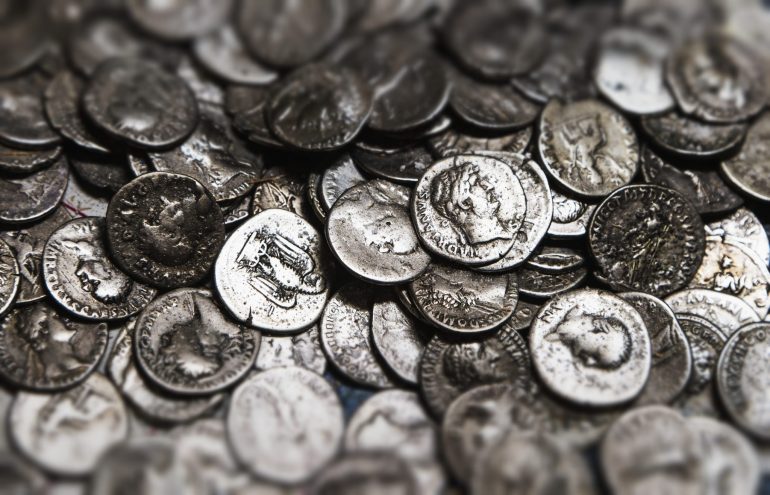
Roman coins in a pile (Photo: John Short / Design Pics via Getty Images)
The Romans used two processes to make coins – cold striking and hot striking.
Cold striking involved literally striking flat discs from a sheet of metal which were then smoothed. Hot striking involved heating the metal and pouring the molten liquid into moulds. The blank coins were then stamped from sheets of softened metal.
Heavy metal stamps known as dies were engraved with the relevant detail, on one side usually a portrait of a Roman emperor, surrounded by text, and on the reverse sometimes a famous battle scene or a religious message or icon with the city of manufacture. To impress the images onto the blank coins one worker would clamp the coin into the die and another would hammer it down to make the impression.
This answers the question ‘how were Roman coins made’ and now, we’ll tell you all about how coins are made today.
Ker-ching! Making Modern Money
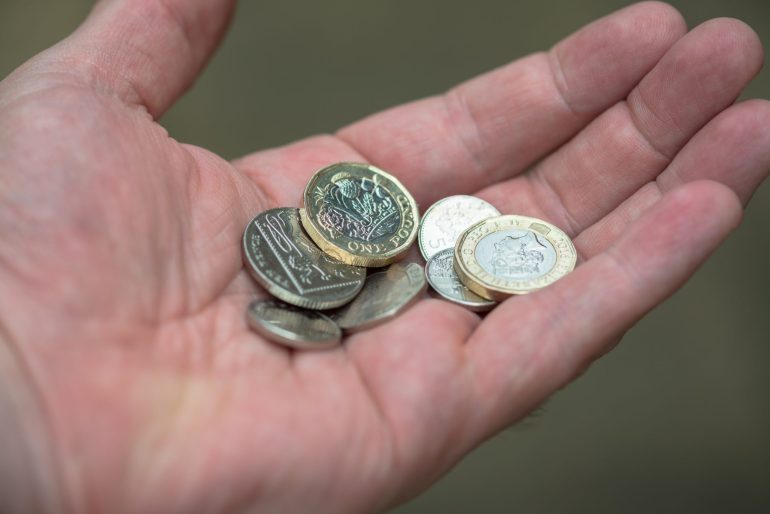
Loose change (Photo: Tim Grist Photography via Getty Images)
Today’s coin manufacturing process starts with the design. Usually, a number of designs are submitted either by invitation or competition. Once the winning design has been selected, a clay model is made which is usually between three and twelve times larger than the coin that eventually ends up in your pocket.
Next, a plaster cast is made, the details are sharpened and then a rubber mould is created using a liquid epoxy resin. From this version, a digital copy is made which is then used to press two ‘actual size’ steel coins – the front side and the reverse side – and these are known as the master dies.
How Coins are Made - The Metal
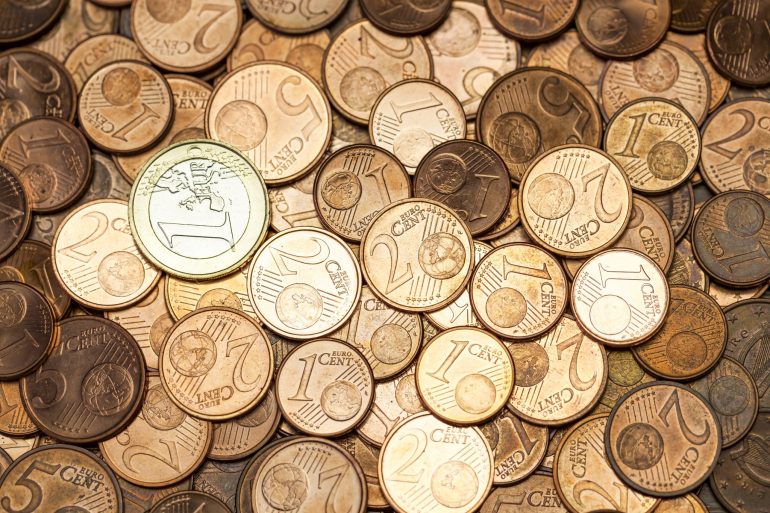
Foreign Coins (Photo: mikroman6 via Getty Images)
As you’ll know, coins are made from different combinations of metal. As an example, if the mint is making 10 pence pieces, the metal is nickel-plated steel which is 94% steel and 6% nickel.
The metal is supplied in huge rolls and is heat-treated at temperatures of up to 950°C to make it softer and more pliable (a process known as annealing). It’s rolled to the thickness of the coin being pressed and then 10p-sized discs called blanks are pressed from the roll.
The blanks are annealed for a second time, washed and dried and then put through a machine called a riddler with slots that perfectly fit the coin being made. If any are too small or too big, they are picked off.
How Coins are Made - Pressing
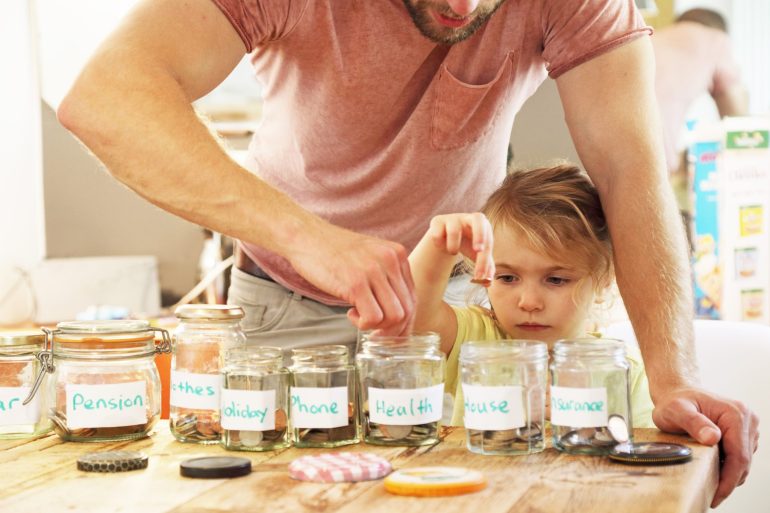
Putting money into savings jars (Photo: Peter Cade via Getty Images)
This is where the magic happens. The master dies for the front and reverse sides of the coin are loaded into a very heavy press and as each blank passes through, they are stamped from both sides using a force of almost 200 tons. Single-striking presses can produce around 400 coins every minute.
Once the finished coins have been pressed, they are filtered through the riddler for a second time to ensure each coin is the perfect size and weight. For a final check, individual coins from each batch are inspected by expertly-trained hands and eyes.
How Coins are Made - Quality Control
The coin manufacturing process is very carefully monitored through the entire journey. The chemical composition of the metal is analysed, the surface, weight, circumference and diameter of the blanks is checked for consistency and the final products are signed off. At this stage they are wrapped and sent out to distribution centres. Finally they end up in high street banks to enter circulation, thus concluding the coin manufacturing process.