According to popular culture, it’s either happiness or money that makes the world go round, when in fact it’s actually springs.
Springs are (usually) metal devices that store energy and provide compression or tension, and have become a crucial component of modern life as we know it. So how are springs actually made? You’re about to find out.
Springs - A Short History
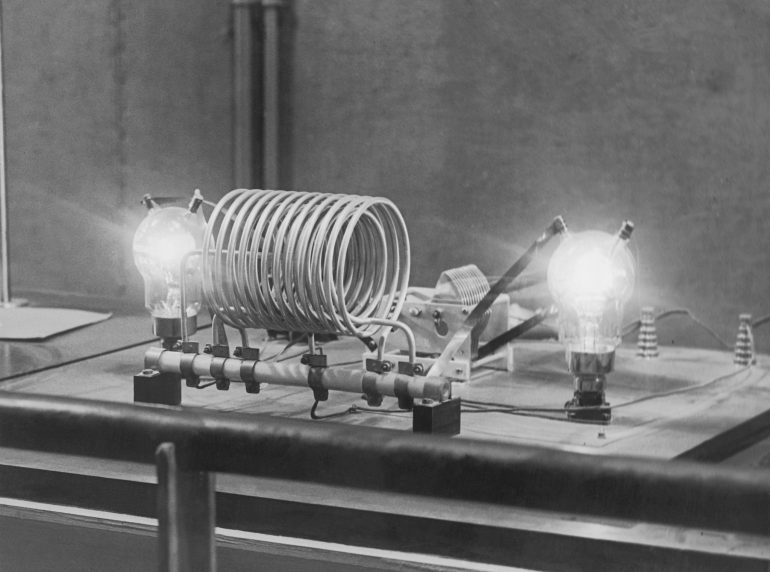
An electrical experiment using a large spring (Photo: FPG via Getty Images)
Before we answer the questions ‘how are coil springs made’ and ‘how are compression springs made’, here’s a little background.
Springs have been used throughout history. From the earliest bows and arrows to Egyptian chariots who used a primitive form of shock absorbers, through to Leonardo da Vinci’s creation of the spring-loaded pistol. Springs make our lives much, much easier.
Spring-powered clocks were first used in the fifteenth century, and in the eighteenth century the French used leaf springs to make horse-drawn carriage rides more comfortable. The Industrial Revolution simply wouldn’t have happened without springs. Today, they can be made as thin as a human hair or as thick as your arm.
Types of Spring
There are two main types of spring – coil springs, which are also known as compression springs, and extension springs. What each one does is self-explanatory by the name.
Extension springs extend to create resistance to a force pulling on it, for example when you jump on a trampoline, the jumper landing on the surface is the force that extends the springs in opposite directions and then the stored energy pulls them back together again.
Coil, or compression springs compress to absorb vibrations and bumps such as the springs in a mattress or the shock absorbers in a car. The spring is evenly compressed under a load and when the force is removed, it reverts to its original size and shape.
What are Springs made of?
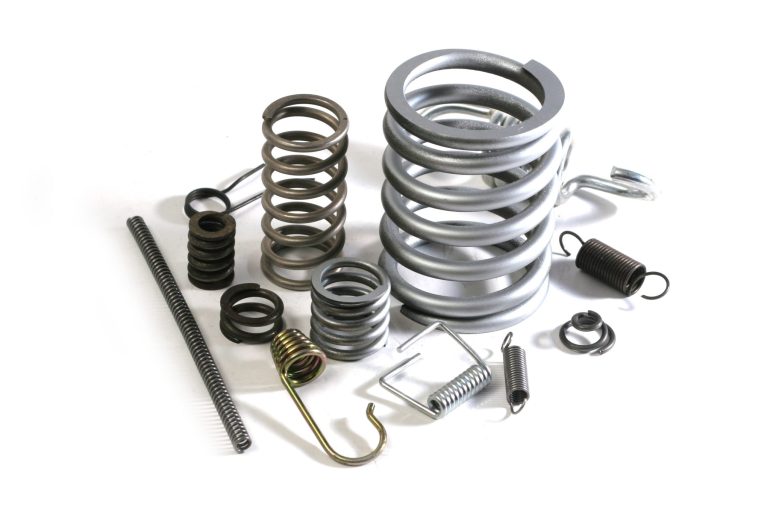
Different types of springs (Photo: maxbmx via Getty Images)
There are three main materials used in the manufacture of springs:
- Stainless steel – this is the most common metal used to make springs, favoured for its versatility and because it’s corrosion-resistant.
- Steel alloy – there are a number of different alloys used to make springs for a variety of purposes including chrome silicon, chrome vanadium and silicon manganese.
- High carbon – for mass production, high carbon springs are very cost-effective and common uses include guitar strings and watch mechanisms.
How are Springs Manufactured?
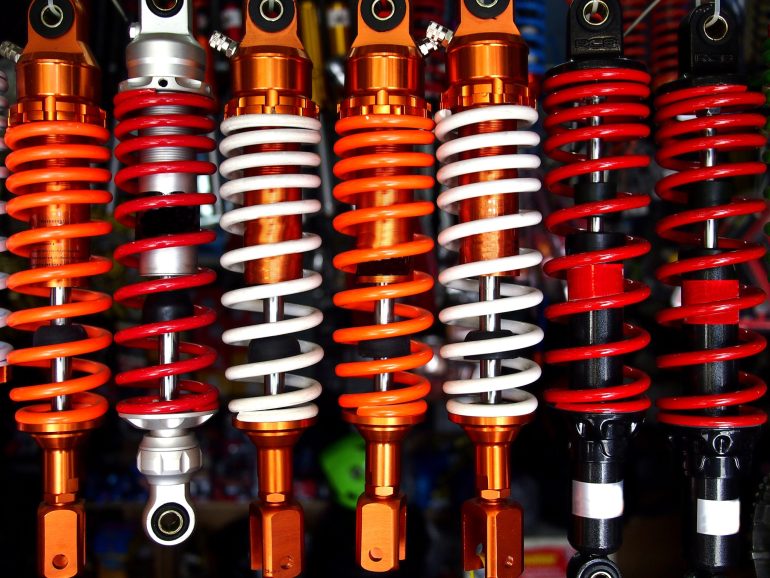
Close-up of colorful spiral metal (Photo: Jun Pinzon / EyeEm via Getty Images)
If you’re looking for the answer to the question ‘how are coil springs made’, here it is.
Stage 1 – The Coiling
It all starts with coiling the metal. Smaller springs, using thinner wire, are coiled around a shaft with the wire at room temperature. Thicker wire is heated to increase its flexibility before being coiled around a shaft in the same way. Once it has been coiled, the spring is removed from the shaft – known as a mandrel – and oil-dipped to cool and harden.
Stage 2 – The Hardening
This is one of the most important elements of the entire spring manufacturing process. Coiling the wire stresses the metal, so it needs to be heat-treated in order for the spring to fully harden and retain its memory. The springs are placed into an oven and the temperature and duration depend on the size of the spring and its material. Modern manufacturing processes typically use a conveyor belt oven. As an example, springs made from music wire are heated to around 260°C for one hour and then left to fully cool.
Stage 3 – The Grinding
If the design requires it, each end of the spring is ground to a flat surface, perpendicular to the sides of the spring. Once this process is complete the springs are released into a large container ready for the next step.
Stage 4 – Shot Peening
This process is undertaken for cold-wired springs. Tiny ball bearings are shot at the springs to smooth the surface and compress and harden the core of the steel.
Stage 5 – The Setting
In answering the question ‘how are compression springs made’, setting is vitally important. Setting involves compressing the springs multiple times so the bordering coils are touching each other. This ensures the spring remains stable throughout its lifecycle.
Stage 6 – The Coating
The springs either go through a process of powder coating or electro-plating. Powder coating prevents rusting and can even be done in different colours. Plating involves covering the surface of the spring with a thin layer of phosphor bronze or titanium to provide increased corrosion resistance, or beryllium copper or gold to ensure the spring can carry an electrical current.
Stage 7 – Quality Control
Before the springs can be packed up and shipped out, they are quality controlled. This will usually involve testing the springs for their intended use and ensuring there are no defective springs in a batch.
So now you know the answer to the age-old question ‘how are springs made’. They are a vital component of almost every mechanical object ever made and without them, our car journeys would be extremely uncomfortable!